鋁型材機架生產的工藝涵蓋擠壓成型、精密切割與表面處理三大關鍵技術,這些環節直接決定了產品的機械性能、尺寸精度及使用壽命。
1. 擠壓成型:結構定型的
擠壓工藝通過將鋁合金圓鑄錠加熱至480-520℃后,在5000-10000噸壓力下迫使鋁液流經精密模具,快速成型為預設截面形狀。模具設計需兼顧截面復雜度與材料流動均勻性,采用H13熱作模具鋼并輔以氮化處理提升壽命。關鍵控制點包括擠壓速度(0.5-15m/min)、溫度梯度與在線淬火工藝,確保型材獲得T5/T6熱處理狀態,抗拉強度可達270MPa以上。
2. 精密切割:尺寸控制的重點
粗切階段采用高速圓鋸床進行±0.5mm精度下料,精加工則運用CNC加工中心實現±0.1mm級公差。對于裝配孔位,采用多軸數控鉆銑設備完成沉孔、螺紋加工,配置激光定位系統確??孜痪取?.05mm。切割后需進行去毛刺處理,避免應力集中影響結構強度。
3. 表面處理:功能與美觀的融合
主流水線采用陽ji氧化(10-25μm膜厚)提升耐蝕性,通過電解著色可定制香檳、黑色等外觀。產品采用電泳涂裝(15-30μm)實現鏡面效果,而粉末噴涂(60-120μm)則適用于戶外場景,耐鹽霧測試可達3000小時。預處理階段包含脫脂、堿蝕、中和三步清洗工藝,確保涂層結合力達0級標準(GB/T9286)。環保型無鉻鈍化技術正逐步替代傳統工藝,滿足RoHS指令要求。
通過工藝參數優化與智能化控制,現代生產線可實現擠壓成品率>92%、切割效率提升40%,表面處理能耗降低30%,終產品兼具輕量化(密度2.7g/cm3)、高強度(6063-T6屈服強度215MPa)與長效防腐特性,廣泛應用于自動化設備、光伏支架及軌道交通領域。
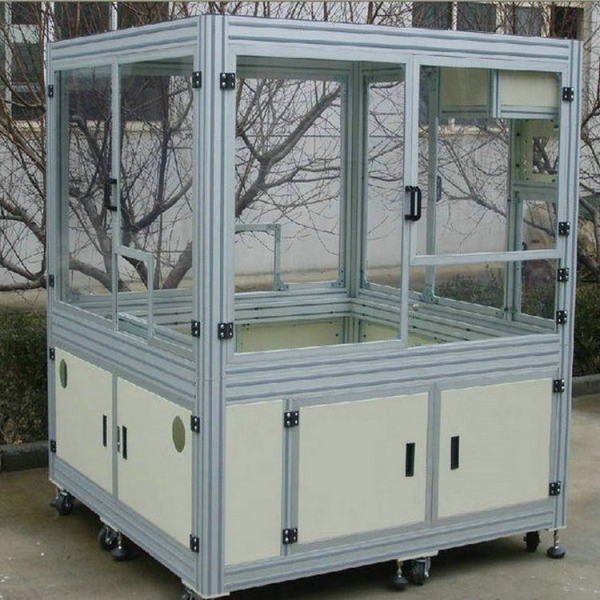